- CNC Surface Wheel Lathe
- CNC Underfloor Wheel Lathe
- CNC Tandem Underfloor Wheel Lathe
- CNC Portal Wheel Lathe
- CNC Vertical Turning & Boring Machine
- CNC Axle Journal Turning and Burnishing Lathe
- Multipurpose Armature machine
- Automated Train Washing Plant
- Rail cum Road Vehicle (Shunter)
- Exclusive Distribution for Products
CNC Surface Wheel Lathe
YSL-08
Max. Main Drive Motor Capacity | 2 x 45 or 55 KW |
Cutting Speed while Profiling | 25 to 80 m/min |
Tool Post Feed for Wheel Profiling | 0.1 to 3.5 mm/rev |
Tool Post Rapid Speed for Both Axes | 3000 mm/min |
Max. Chip Cross Section while Profiling | 20 mm2 |
Cycle Time / Wheel Set | 14-16 min. |
Max. Tread Diameter | 1250mm* |
Min. Tread Diameter | 750mm* |
Wheel Width | 75 to 145mm |
Max. Axle Length | 2750mm* |
Min. Axle Length | 1200mm* |
Max. Weight of Wheel Set | 50 kN |
Max./Min. Dia. for Brake Disc Machining | 700/250mm |
*Depends on track gauge
Wheel Profiling | |
Max. Difference in Dia. of Both Wheels | <0.15mm |
Accuracy of Wheel Profile when Compared with Standard Gauge | <0.2mm |
Radial Run Out of Wheel | <0.2mm |
Axial Run Out of Wheel | <0.2mm |
Profile Surface Finish | <12.5µm Ra |
Brake Disc Machining (Optional) | |
Min. Surface Finish | <2.5µm Ra |
Flatness of Surface | <0.1/100mm |
Lateral Wobble | <0.2mm |
YSL-12
Max. Main Drive Motor Capacity | 2 x 37.5 KW |
Cutting Speed while Profiling | 25 to 80 m/min |
Tool Post Feed for Wheel Profiling | 0.1 to 3.5 mm/rev |
Tool Post Rapid Speed for Both Axes | 3000 mm/min |
Max. Chip Cross Section while Profiling | 16 mm2 |
Cycle Time / Wheel Set | 16-18 min. |
Max. Tread Diameter | 1250mm* |
Min. Tread Diameter | 750 mm* |
Wheel Width | 75 to 145mm |
Max. Axle Length | 2750mm* |
Min. Axle Length | 1200mm* |
Max. Weight of Wheel Set | 50 kN |
Max./Min. Dia. for Brake Disc Machining | 700/250mm |
*Depends on track gauge
Wheel Profiling | |
Max. Difference in Dia. of Both Wheels | <0.3mm |
Accuracy of Wheel Profile when Compared with Standard Gauge | <0.2mm |
Radial Run Out of Wheel | <0.3mm |
Axial Run Out of Wheel | <0.3mm |
Profile Surface Finish | <12.5µm Ra |
Brake Disc Machining (Optional) | |
Min. Surface Finish | <2.5µm Ra |
Flatness of Surface | <0.1/100mm |
Lateral Wobble | <0.3mm |
YSL-21
Max. Main Drive Motor Capacity | 1 x 22 KW |
Cutting Speed while Profiling | 25 to 80 m/min |
Tool Post Feed for Wheel Profiling | 0.1 to 3.5 mm/rev |
Tool Post Rapid Speed for Both Axes | 3000 mm/min |
Max. Chip Cross Section while Profiling | 10 mm2 |
Cycle Time / Wheel Set | 50-60 min. |
Max. Tread Diameter | 1250mm* |
Min. Tread Diameter | 750mm* |
Wheel Width | 75 to 145mm |
Max. Axle Length | 2750mm* |
Min. Axle Length | 1200mm* |
Max. Weight of Wheel Set | 50 kN |
Max./Min. Dia. for Brake Disc Machining | 700/250mm |
*Depends on track gauge
Wheel Profiling | |
Max. Difference in Dia. of Both Wheels | <0.5mm |
Accuracy of Wheel Profile when Compared with Standard Gauge | <0.3mm |
Radial Run Out of Wheel | <0.3mm |
Axial Run Out of Wheel | <0.3mm |
Profile Surface Finish | <12.5µm Ra |
Max./Min. Dia. for Brake Disc Machining on all products and all products pages.
CNC Surface Wheel Lathe is an automatic machine for simultaneous re-profiling new or worn-out wheels when disassembled from railway vehicles like locomotives, electrical and diesel multiple units, coaches, wagons, metro & tram coaches.
Pl. note that improvements is a continuous process. Hence, details explained above may undergo some changes meeting functional, quality and productivity requirements of the required technical specification.
CNC Underfloor Wheel Lathe
YUL -08
Max. Main Drive Motor Capacity | 4 x 15 KW |
Cutting Speed while Profiling | 25 to 80 m/min |
Tool Post Feed for Wheel Profiling | 0.1 to 2.5 mm/rev |
Tool Post Rapid Speed for Both Axes | 3000 mm/min |
Max. Chip Cross Section while Profiling | 10 mm2 |
Max. Tread Diameter | 1500 mm* |
Min. Tread Diameter | 540mm* |
Wheel Width | 75 to 145mm |
Max. Width of Vehicle (Rolling Stock) | 3600/3100 mm* |
Min. Width of Vehicle (Rolling Stock) | 2900/2400 mm* |
Max. Axle Length | 2750mm* |
Min. Axle Length | 1200mm* |
Max. Axle Load | 300/400 kN |
Max./Min. Dia. for Brake Disc Machining | 700/250mm |
*Depends on track gauge
Wheel Profiling | |
Max. Difference in Dia. of Both Wheels | <0.1mm |
Accuracy of Wheel Profile when Compared with Standard Gauge | <0.2mm |
Radial Run Out of Wheel | <0.1mm |
Axial Run Out of Wheel | <0.15mm |
Profile Surface Finish | <12.5µm Ra |
Brake Disc Machining (Optional) | |
Min. Surface Finish | <2.5µm Ra |
Flatness of Surface | <0.1/100mm |
Lateral Wobble | <0.2mm |
This system enhances maintenance efficiency and minimizes downtime, making it an ideal solution for railway wheelset management.
Pl. note that improvements is a continuous process. Hence, details explained above may undergo some changes meeting functional, quality and productivity requirements of the required technical specification.
CNC Tandem Underfloor Wheel Lathe
A combination of two machines working in synchronised tandem mode
YUL -12T
Max. Main Drive Motor Capacity | 4 Motors of 15 KW capacity each |
Cutting Speed while Profiling | 20 to 120 m/min |
Cutting Speed while Brake Disc Machining | 120 m/min (Constant) |
Tool Post Feed for Wheel Profiling | 0.1 to 2.5 mm/rev |
Tool Post Rapid Speed for Both Axes | 3000 mm/min |
Max. Chip Cross Section while Profiling | 10 mm2 |
Max. Tread Diameter | 1500mm* |
Min. Tread Diameter | 540mm* |
Wheel Width | 75 to 155mm |
Max. Axle Load | 300/400 KN |
Max. Width of Vehicle (Rolling Stock) | 3600/3100 mm* |
Min. Width of Vehicle (Rolling Stock) | 2900/2400 mm* |
Max. Axle Length | 2750mm* |
Min. Axle Length | 1200mm* |
Max./Min. Dia. for Brake Disc Machining | 700/250mm |
*Depends on track gauge
Wheel Profiling | |
Difference in Dia. of Both Wheels | <0.10mm |
Accuracy of Wheel Profile when Compared with Standard Gauge | <0.2mm |
Radial Run Out of Wheel | <0.10mm |
Axial Run Out of Wheel | <0.15mm |
Profile Surface Finish | <12.5µm Ra |
Brake Disc Machining (Optional) | |
Surface Finish | <2.5µm Ra |
Flatness of Surface | <0.1/100mm |
Lateral Wobble | <0.2mm |
Advanced Wheel-Turning Machine Features
- Versatile Operation: One machine is fixed while the other is moveable, allowing easy accommodation of varying wheelbases of bogies.
- Shared Rail System: Both machines operate on a common rail system, with individual hydraulic and pneumatic systems, ensuring flexibility and efficiency.
- Independent Functionality: Each machine can work individually, enabling the profiling of a single wheel set when required.
- Robust Construction: Rigid cast iron basements provide solid support for both the mobile and fixed machines, ensuring stability during operations.
- Precision Motion: The mobile machine moves along linear motion guideways with pre-loaded ball screws, controlled by a CNC system for smooth, precise movement.
- Synchronized and De-synchronized Mode: All four drive rollers of both machines rise in synchronized mode with displacement feedback during lifting and centering of the wheel set. In de-synchronized follow-up mode during wheel profile turning, the rollers maintain positive contact even on worn wheels.
- Slippage Detection: The system includes a feature to detect slippage between the drive rollers and the wheel set, enhancing reliability.
- Dual CNC Tool Carriages: Each machine is equipped with two CNC tool carriages, enabling simultaneous measuring and machining of both wheels in a wheel set.
- High-Precision Mechanics: Hardened and ground guideways, along with preloaded ball screws, ensure consistently high accuracy.
- Quick-Change Tooling: Equipped with CAPTO/KM LOCK quick-change tooling for rapid wheel profiling and brake disk machining, minimizing downtime.
Integrated Measurement System: Each CNC tool carriage comes with a proven wheel profile and diameter measuring unit for pre- and post-machining measurement, ensuring precision throughout the process.
Maximizing Efficiency with Tandem UFWL Wheel Profiling
- Significant Time Reduction: Our advanced wheel profiling system reduces the re-profiling time for coaches by 50% and for locomotives by 33%, ensuring quicker turnaround and higher availability for revenue service.
- Simplified Maintenance: Isolating and replacing a non-usable or “sick” coach is a time-consuming process. With our Tandem Underfloor Wheel Lathe (UFWL), entire trains can be brought in for wheel profiling, allowing the process to be completed in less than 2 hours per coach.
Pl. note that improvements is a continuous process. Hence, details explained above may undergo some changes meeting functional, quality and productivity requirements of the required technical specification.
CNC Portal Wheel Lathe
YPL -02
Max. Main Drive Motor Capacity | 2 x 55 KW |
Cutting Speed while Profiling | 25 to 80 m/min |
Tool Post Feed for Wheel Profiling | 0.1 to 4 mm/rev |
Tool Post Rapid Speed for Both Axes | 4500 mm/min |
Max. Chip Cross Section while Profiling | 32 – 50 mm2 |
Cycle Time / wheelset | 8 – 12 mins |
Max. Tread Diameter | 1250mm* |
Min. Tread Diameter | 750mm* |
Wheel Width | 75 to 145mm |
Max. Axle Length | 2750mm* |
Min. Axle Length | 1850mm* |
Max. Weight of Wheelset | 50 KN |
Max./Min. Dia. for Brake Disc Machining | 700/250mm |
*Depends on track gauge
Wheel Profiling | |
Max. Difference in Dia. of Both Wheels | <0.15mm |
Accuracy of Wheel Profile when Compared with Standard Gauge | <0.2mm |
Radial Run Out of Wheel | <0.1mm |
Axial Run Out of Wheel | <0.2mm |
Profile Surface Finish | <12.5µm Ra |
Brake Disc Machining (Optional) | |
Min. Surface Finish | <2.5µm Ra |
Flatness of Surface | <0.1/100mm |
Lateral Wobble | <0.2mm |
CNC Portal Wheel Lathe: Precision and Efficiency in Wheel Re-Profiling
- Automatic Roll-Through Design: The CNC Portal Wheel Lathe features an automatic, portal-style construction with roll-through movement, ideal for efficient handling of wheel sets.
- Versatile Application: It is suitable for simultaneous re-profiling of both new and worn wheels, disassembled from various railway vehicles, including locomotives, electric and diesel multiple units, coaches, wagons, metro, and tram coaches.
Robust Performance: This extremely rigid machine can handle depth cuts ranging from a minimum of 0.5 mm to a maximum of 12 mm on both wheels of a set, ensuring precise and efficient re-profiling in a single operation.
Pl. note that improvements is a continuous process. Hence, details explained above may undergo some changes meeting functional, quality and productivity requirements of the required technical specification.
CNC Vertical Turning & Boring Machine
YVM -04
Turning / swing diameter | 1600mm |
Table diameter | 1400mm |
Table speed | from 3 to300rpm |
Turning height | 600mm |
Vertical travel of the ram head | 700mm |
Table Drive Motor Capacity | 45KW |
Horizontal traverse of ram head | +900/-50 mm |
Rapid traverse rate | 8000 mm/min |
Ram cross section | 200 x 200 or 250 x 250 mm |
Surface finish while boring | Ra 0.8 micron |
Surface finish while turning | Ra 1.6 micron |
Surface finish while facing | Ra 1.6 micron |
Machine accuracies – As per ISO:3655 | |
Vertical & horizontal travel of ram laser calibrated as per VDI DGQ 3441 |
CNC Vertical Turning and Boring Machine: Versatility for Railway Wheel Machining
- Comprehensive Wheel Machining: This machine is ideal for railway wheel front and back profile machining, hub boring and facing, rim front and back facing, as well as tread and flange profile turning.
- Precision Grooving: It is designed for a wide range of grooving operations, ensuring high precision across various wheel components.
Optional Live Spindle: With the optional live spindle, additional operations such as drilling, tapping, and brake disc mounting hole machining can be efficiently performed, adding versatility to the machine’s capabilities.
Pl. note that improvements is a continuous process. Hence, details explained above may undergo some changes meeting functional, quality and productivity requirements of the required technical specification.
CNC Axle Journal Turning & Burnishing Lathe
YTB – 04
Main Drive Motor Capacity | 11 KW |
Cutting Speed for Axle Turning & Burnishing | 50 to 400 m/mins. |
Tool Post Feed for Axle Turning & Burnishing | 0.1 to 2.5 mm/rev |
Max. depth of cut while axle turning | 2 mm. |
Max. Tread Diameter | 1250mm* |
Min. Tread Diameter | 540mm* |
Wheel Width | 75 to 145mm |
Max. Axle Length | 2750mm* |
Min. Axle Length | 1200mm* |
Max. weight of wheel set | 50 kN |
Min. – Max. Axle Journal diameter | 70-320 mm |
Min. – Max. Axle Journal length | 110 – 480mm |
Ovality of journal | <0.01mm |
Taper of journal | <0.01/100mm |
Surface finish of journal after burnishing | <0.2 µm Ra |
Note: Continuous Improvement Commitment We are dedicated to continuous improvement, and as such, the details outlined above may be subject to modifications to further enhance functionality, quality, and productivity, in alignment with the specific technical requirements of your project.
Multipurpose Armature machine
YMM – 04
Main Drive Motor Capacity | 15 KW |
Carriage Rapid Traverse in Longitudinal Direction | 600 mm/min |
Head Stock Spindle Speed – Infinitely Variable | 1.5 to 300 rpm |
Carriage Feed in Longitudinal Direction | 0 to 100 mm/min |
Maximum Depth of Cut while Commutator Turning | 2.5 mm |
Maximum Banding Tension during Wire/Tape Banding | 300 Kg |
Armature | |
Maximum Armature Weight | 30 KN |
Minimum Length Of Armature | 500 mm |
Maximum Length of Armature | 1600 mm |
Minimum Diameter of Armature | 500 mm |
Maximum Diameter of Armature | 1400 mm |
Commutator | |
Minimum Diameter of Commutator to be Machined | 200 mm |
Maximum Diameter of Commutator to be Machined | 900 mm |
Minimum Length of Commutator to be Machined | 75 mm |
Maximum Length of Commutator to be Machined | 450 mm |
Accuracies | |
Ovality of Commutator Turning | <0.015 mm* |
Taper of Commutator Turning | <0.015 mm* |
Uniformity of Banding Tension | <±10 Kg |
Pl. note that improvements is a continuous process. Hence, details explained above may undergo some changes meeting functional, quality and productivity requirements of the required technical specification.
Automated Train Washing Plant
Train wash speed through plant | 3 to 5 KMPH |
Fresh water requirement | Max. 60 litres per coach / car |
Pressure of spray at nozzle outlet at final stage | Approx. 10Kg/sq.cm |
Total width of the support structures stands along with cleaning implements etc. installed on the railway track | 5.5 meters (Max.) |
Power Supply | 415V±10%, 50Hz±3% |
Length of straight track between fouling marks | 50 Mtrs. (Max.) |
Productivity | The end-to-end cycle time for cleaning a train for 24 coaches will not be more than 15 minutes. |
- Automatic Washing Cycle: The system handles the entire cleaning process while the train moves at a speed of 3-5 kmph, which includes:
- Pre-wetting/rinsing
- Spraying detergent
- Multiple brushing stations
- Final rinsing
- Mopping for a spotless finish
- Water Conservation: We prioritize sustainability! The system recycles water through an effluent treatment plant, promoting eco-friendly operation while conserving water.
- Precision with Technology: Optical laser sensors detect the entry and speed of the railcars, ensuring an optimized and seamless washing cycle.
- Modular and Robust Design: Built to last, our plant features a modular construction, offering flexibility and durability with low operation and maintenance costs.
Note: Continuous Improvement Commitment We are dedicated to continuous improvement, and as such, the details outlined above may be subject to modifications to further enhance functionality, quality, and productivity, in alignment with the specific technical requirements of your project.
Rail Based Loco Shunter
KRE 15 RCRV
Type | Rail cum road vehicle |
Service weight | 6 t +/- 10% |
Max wheel load | Approx. 1.5T |
Gauge | 1676 mm / 1435 mm |
Max. Speed | V1 loaded 0 – 2 km/hr V2 solo 0 – 4 km/hr |
Max. tract. effort | 15 kN at wheel rim at adhesion µ =0.5 in dry (0.3 in wet) |
Towing capacity | 135T locomotive / other rolling stock at gradient from 0-2.5 per 1000. |
Wheelbase | 1880 mm |
Width | 2300 (2420) mm / 2060 (2180) mm |
Height | max 1420 (1560mm including antenna) mm for visibility |
Total length (without couplers) | 3080 mm |
For Up railing | approx. 3.5m x 3.5m |
Guiding wheels | 4 Nos. Steel flanged wheel, profile according to IR. CSL – 3040 or UIC 510, dia. 330mm |
Traction / steering wheels | 4 Nos. Vulkolan / Polyurethane dia. 304 x 140 mm |
Steering | 4-wheel: -crab side way, -perpendicular, -circular, -360 degrees rotating on own axis |
Battery capacity | 80V, 460Ah waterless, with electrolyte mixing for less maintenance |
Battery charger | Charging time max 10 hours, 415V, 3 Phase + earth, fused at 16A |
E-system | 24 V PLC Iqan |
Safety Integrity Level | SIL 3 |
OPTIONAL : Coupler as per requirement
Joint Manufacturing with BEMO Rail, Netherland. Pl. note that improvements is a continuous process. Hence, details explained above may undergo some changes meeting functional, quality and productivity requirements of the required technical specification.
Exclusive distribution for products of SKC GLEITTECHNIK GMBH, Germany
SKC, a German technology company is the pioneer in the production and use of malleable viscous materials and a 35 year old company. High quality materials with quality management system according DIN EN ISO 9001.
Products : SKC compounds are two-component materials based on high quality epoxy resins. Various fillers and additives enable a tailor-made adaptation of the materials to the specific
- SLIDEWAY COATINGS (SKC 3, SKC 60, SKC 62, SKC 63, SKC 63 R, SKC 90, SKC 400 ELF)
- COATINGS WITH JOINT FACES (SKC 53, SKC 55, SKC 57, SKC 58)
- RELEASING COMPOUND (SKC 15 Releasing Compound, SKC 12 TRS Release Spray, SKC 14 Silicon Releasing Compound, SKC 14 TRS Release Spray, SKC 13 W Release Wax)
- ACCESSORIES
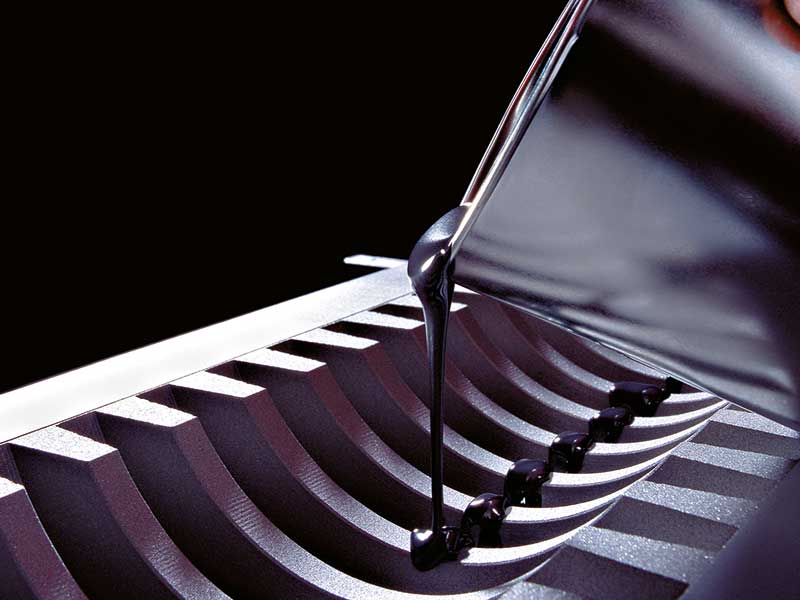