CNC Tandem Underfloor Wheel Lathe
A combination of two machines working in synchronised tandem mode
YUL -12T
Technical Data of Machine
Max. Main Drive Motor Capacity | 4 Motors of 15 KW capacity each |
Cutting Speed while Profiling | 20 to 120 m/min |
Cutting Speed while Brake Disc Machining | 120 m/min (Constant) |
Tool Post Feed for Wheel Profiling | 0.1 to 2.5 mm/rev |
Tool Post Rapid Speed for Both Axes | 3000 mm/min |
Max. Chip Cross Section while Profiling | 10 mm2 |
Wheel Set Data for Machining
Max. Tread Diameter | 1500mm* |
Min. Tread Diameter | 540mm* |
Wheel Width | 75 to 155mm |
Max. Axle Load | 300/400 KN |
Max. Width of Vehicle (Rolling Stock) | 3600/3100 mm* |
Min. Width of Vehicle (Rolling Stock) | 2900/2400 mm* |
Max. Axle Length | 2750mm* |
Min. Axle Length | 1200mm* |
Max./Min. Dia. for Brake Disc Machining | 700/250mm |
*Depends on track gauge
Accuracies of Wheel Set
Wheel Profiling | |
Difference in Dia. of Both Wheels | <0.10mm |
Accuracy of Wheel Profile when Compared with Standard Gauge | <0.2mm |
Radial Run Out of Wheel | <0.10mm |
Axial Run Out of Wheel | <0.15mm |
Profile Surface Finish | <12.5µm Ra |
Brake Disc Machining (Optional) | |
Surface Finish | <2.5µm Ra |
Flatness of Surface | <0.1/100mm |
Lateral Wobble | <0.2mm |
Features
Advanced Wheel-Turning Machine Features
- Versatile Operation: One machine is fixed while the other is moveable, allowing easy accommodation of varying wheelbases of bogies.
- Shared Rail System: Both machines operate on a common rail system, with individual hydraulic and pneumatic systems, ensuring flexibility and efficiency.
- Independent Functionality: Each machine can work individually, enabling the profiling of a single wheel set when required.
- Robust Construction: Rigid cast iron basements provide solid support for both the mobile and fixed machines, ensuring stability during operations.
- Precision Motion: The mobile machine moves along linear motion guideways with pre-loaded ball screws, controlled by a CNC system for smooth, precise movement.
- Synchronized and De-synchronized Mode: All four drive rollers of both machines rise in synchronized mode with displacement feedback during lifting and centering of the wheel set. In de-synchronized follow-up mode during wheel profile turning, the rollers maintain positive contact even on worn wheels.
- Slippage Detection: The system includes a feature to detect slippage between the drive rollers and the wheel set, enhancing reliability.
- Dual CNC Tool Carriages: Each machine is equipped with two CNC tool carriages, enabling simultaneous measuring and machining of both wheels in a wheel set.
- High-Precision Mechanics: Hardened and ground guideways, along with preloaded ball screws, ensure consistently high accuracy.
- Quick-Change Tooling: Equipped with CAPTO/KM LOCK quick-change tooling for rapid wheel profiling and brake disk machining, minimizing downtime.
Integrated Measurement System: Each CNC tool carriage comes with a proven wheel profile and diameter measuring unit for pre- and post-machining measurement, ensuring precision throughout the process.
Benefits
Maximizing Efficiency with Tandem UFWL Wheel Profiling
- Significant Time Reduction: Our advanced wheel profiling system reduces the re-profiling time for coaches by 50% and for locomotives by 33%, ensuring quicker turnaround and higher availability for revenue service.
- Simplified Maintenance: Isolating and replacing a non-usable or “sick” coach is a time-consuming process. With our Tandem Underfloor Wheel Lathe (UFWL), entire trains can be brought in for wheel profiling, allowing the process to be completed in less than 2 hours per coach.
Pl. note that improvements is a continuous process. Hence, details explained above may undergo some changes meeting functional, quality and productivity requirements of the required technical specification.
Why you choose us for your next project!
- Individual CNC latest System communicating with each other for both the machines.
- Box structured cast construction for extreme rigidity, vibration damping and consistent accuracy for structural elements subjected to cutting loads.
- Particularly, when coach can not be separated due to train set formulation, the holding time of entire train is reduced to half with tandem UFWL.
- Equipped with Latest Industry 4.0 features.
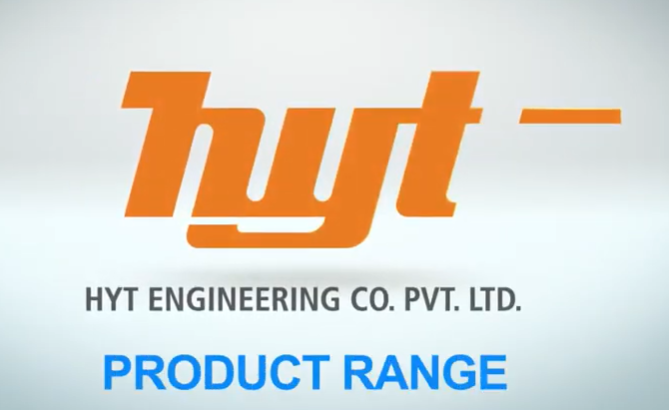
Play Video